Fasteners and Machining: Enhancing Toughness and Performance in Production
Fasteners and Machining: Enhancing Toughness and Performance in Production
Blog Article
Browsing the World of Fasteners and Machining: Strategies for Precision and Speed
In the intricate realm of bolts and machining, the pursuit for precision and speed is a continuous obstacle that demands careful interest to information and tactical planning. From comprehending the diverse selection of fastener types to picking optimum materials that can stand up to strenuous demands, each action in the procedure plays a critical function in attaining the desired result. Accuracy machining strategies further raise the intricacy of this craft, needing a delicate balance between technical proficiency and ingenious strategies. As we delve into the methods that can improve both speed and effectiveness in this domain name, the interaction between high quality control procedures and functional excellence emerges as a critical focal point.
Understanding Fastener Types
When selecting bolts for a project, comprehending the numerous kinds offered is crucial for making sure optimum performance and dependability. Screws are used with nuts to hold materials with each other, while screws are flexible fasteners that can be made use of with or without a nut, depending on the application. Washers are necessary for dispersing the load of the fastener and protecting against damage to the material being attached.
Picking the Right Materials
Comprehending the relevance of selecting the best materials is vital in ensuring the optimal performance and dependability of the picked bolt kinds discussed previously. When it pertains to bolts and machining applications, the product option plays an essential function in figuring out the total toughness, durability, corrosion resistance, and compatibility with the designated atmosphere. Different materials provide varying residential or commercial properties that can considerably affect the performance of the fasteners.
Typical products made use of for bolts consist of steel, stainless steel, brass, aluminum, and titanium, each having its special toughness and weak points. Steel is renowned for its high toughness and durability, making it suitable for a large range of applications. Stainless-steel supplies exceptional rust resistance, suitable for environments vulnerable to moisture and chemicals. Light weight aluminum is light-weight and corrosion-resistant, making it suitable for applications where weight reduction is essential. Brass is frequently chosen for its visual allure and exceptional conductivity. Titanium is understood for its exceptional strength-to-weight proportion, making it excellent for high-performance applications. Selecting the right product includes considering aspects such as strength demands, ecological problems, and budget restraints to make sure the desired efficiency and longevity of the bolts.
Precision Machining Techniques
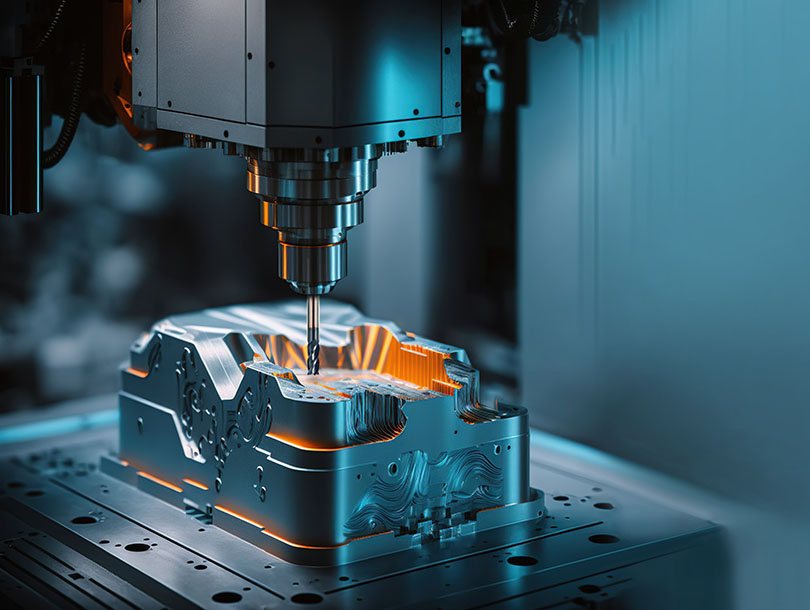
Along with CNC machining, various other accuracy methods like grinding, transforming, milling, and drilling play essential functions in bolt production. Grinding aids achieve great surface coatings and tight dimensional resistances, while turning is typically made use of to create cylindrical parts with precise diameters. Milling and boring procedures are vital for forming and creating holes in fasteners, guaranteeing they fulfill exact specifications and function properly.
Enhancing Rate and Efficiency
To optimize fastener production procedures, it is necessary to streamline operations and execute efficient methods that enhance accuracy machining techniques. One key technique for improving rate and effectiveness is the application of lean production concepts. By lowering waste and this article concentrating on constant enhancement, lean techniques aid eliminate bottlenecks and maximize workflow. Furthermore, purchasing automation innovations can dramatically enhance manufacturing rate. Automated systems can take care of recurring jobs with accuracy and rate, enabling employees to concentrate on even more complicated and value-added tasks. Taking On Just-In-Time (JIT) supply administration can also improve efficiency by guaranteeing that the best materials are available at the correct time, minimizing excess supply and lowering preparations. Additionally, fostering a society of cooperation and interaction among staff member can improve overall effectiveness by advertising openness, analytical, and advancement. By integrating these techniques, makers can achieve an equilibrium between rate and precision, inevitably enhancing their affordable edge in additional reading the bolt market.
Quality Assurance Measures
Applying rigorous high quality control actions is important in making certain the reliability and consistency of bolt items in the manufacturing procedure. Quality control steps include numerous phases, starting from the selection of basic materials to the last examination of the finished fasteners. One essential element of quality control is carrying out detailed material evaluations to confirm compliance with requirements. This includes examining variables such as material stamina, structure, and longevity to assure that the bolts satisfy market standards. Additionally, keeping an eye on the machining processes is vital to support dimensional accuracy and surface finish quality. Utilizing advanced innovation, such as computerized examination systems and accuracy measuring tools, can enhance the precision and performance of quality assurance procedures.
Regular calibration of equipment and machinery is essential to maintain consistency in manufacturing and make certain that bolts fulfill the required resistances. Implementing strict procedures for identifying and attending to non-conformities or problems is essential in protecting against substandard products from entering the market. By establishing a thorough quality control structure, manufacturers can support the track record of their brand name and supply fasteners that meet the greatest requirements of efficiency and longevity.
Conclusion

In the detailed realm of fasteners and machining, the mission for accuracy and speed is a perpetual challenge that demands meticulous attention to detail and strategic planning. When it comes to fasteners and machining applications, the product option plays a critical duty in determining the total toughness, longevity, deterioration resistance, and compatibility with the desired setting. Accuracy machining includes different innovative approaches that ensure the tight tolerances and specifications required for bolts.In enhancement to CNC machining, various other accuracy methods like grinding, turning, milling, and boring play important functions in fastener production.To optimize fastener manufacturing procedures, it is necessary to enhance operations and implement effective techniques that complement precision machining techniques.
Report this page